Uploaded: Mon, Feb 6, 2023, 11:35 am 0 Time to read: about 4 minutes
The framing system for Bone Structure homes is made of steel tubes manufactured in factories and designed to connect together on-site. Photo courtesy Bone Structure. Switches
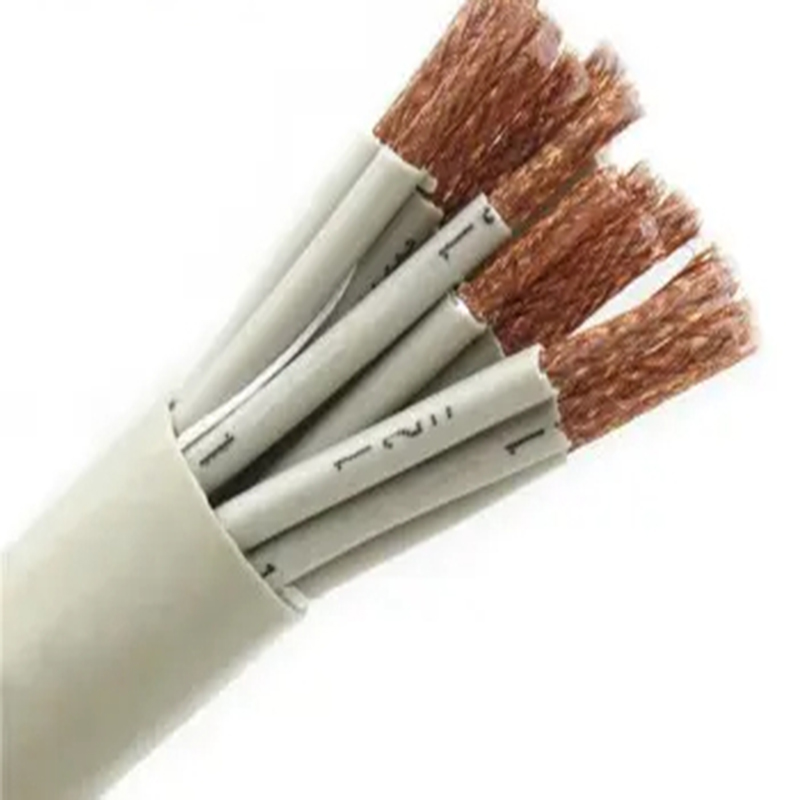
It was the aspiration of Stanford's Atmosphere and Energy Program director
to live in a net-zero home that was "strong, durable and could withstand a major earthquake, as well as termites and mold," that brought Canadian homebuilder Marc Bovet to Stanford in 2016 to build his first home in the state made of recycled steel. The prefab steel frame pieces arrived in one truckload from
Canada and were snapped together in less than a week, creating the shell for Mark Jacobson's new 3,000-square-foot home, which reportedly cost an estimated $1.5 million.
Solar panels coupled with Tesla Powerwall battery packs were installed to produce enough electricity to power the entire house plus two cars.
Marc Bovet. Courtesy Bone Structure.
Since then, Bovet has exhibited steely determination to shake up the North American home market with steel frame, custom-built homes manufactured by his family-operated business, Bone Structure. Bovet now employs a staff of 40 architects, engineers, technologists and urban planners and operates a satellite office in San Francisco in addition to the company's Laval headquarters in Quebec, Canada. He has built hundreds of homes coast to coast in Canada and throughout California, including about two dozen along the Midpeninsula in Palo Alto, Menlo Park and Atherton.
Help sustain the local news you depend on.
Your contribution matters. Become a member today.
Bovet, who founded Bone Structure in 2005, said the company's steel construction system "just made sense." The goal, he said, is to create "homes that are not just energy efficient, but comfortable."
Once on-site, steel pieces snap together like toy erector sets
A carpenter installs window supports in the company's first California house under construction at Stanford in 2016. Photo by Veronica Weber.
The company's homes are built from steel tubes manufactured in factories and designed to be attached together on-site.
The framing system used in the homes is 88% recycled steel, mostly made of smashed cars. Each Bone Structure house is custom-designed and built with modular components, with no interior bearing walls.
Bovet said homes range in size from 600 to 22,000 square feet. Bone Structure designs and plans homes for its owners, who then work with local builders and contractors to construct the homes, Bovet explained.
Assembled in pre-built sections and then delivered to the construction site, Bovet likens the building process as similar to using such toys as erector sets
or Legos. The horizontal steel pieces snap into place and are strong enough to support the interior finishes, including Sheetrock or tile, he said.
Bovet said the pre-assembled sections have clear connections for specialists like plumbers and electricians to follow for their part in the construction.
The pieces are "heavily engineered. All components are laser cut," said Bovet's son Charles, who received his master's degree in civil and environmental engineering and construction from Stanford University in 2013 and now serves as the company's vice president of business development.
He noted that they use a patented "ankle" that allows some wiggle room in fitting those precisely cut components into the poured-concrete foundation.
Steel framing is exposed during construction of Bone Structure's first residential project built in the state at Stanford in 2016. Photo by Veronica Weber.
While the homes lend themselves to modern designs with long beam spans, the company's homes can be finished in stucco, brick or wood siding. The insulation, a combination of polystyrene panels and spray foam, are applied to the outside steel frame of the home and then covered up with whatever material the architect calls for.
The plumbing and electrical infrastructure can be "threaded" through the steel frames through pre-cut holes. Bovet said he didn't start out using steel when he first entered the homebuilding sector.
When he founded Bone Structure, Bovet used conventional building materials in his first project, but an unsuccessful launch led him to seek inspiration from above — literally — to move forward with his fledgling business.
"I was driving near the (Montreal) airport when a jet thundered overhead," Bovet said, recalling his trip down a highway past Trudeau International Airport. "It occurred to me as it successfully took flight that the plane was not made of wood, but steel."
He seized upon that inspiration.
This rendering shows how a Bone Structure home still under construction in Palo Alto will look when finished. Image courtesy Bone Structure.
After "a lot of trial and error," Bovet said his company settled on the use of steel-frame residential structures, which he says avoids such wood structure deterioration problems like termites and mold, is more seismically safe, fire and flood resistant, and sustainable. Since the "bones" of his homes contain 88% recycled steel, the construction process does not create mountains of waste typical of conventional building sites, he added.
Superior levels of energy efficiency are achieved through airtight insulation by combining rigid and foam insulation materials that can reduce heating and cooling costs by up to 90% compared to traditional construction, according to company information.
Another distinctive feature of Bone Structure homes are floor-to-ceiling windows that afford sweeping views and accentuate the soya-based polyurethane insulation "thermal envelope" that reduces energy use, Bovet said.
He views the Bone Structure process as a simplified one that makes the home-building experience a less stressful one for homeowners. Over the past seven years, Bone Structure has seen demand for their homes increase along the Midpeninsula. The company recently revealed its newest local structure to the public on Wilson Street in Palo Alto this past November. During the three-day open house for the two-story home, Bovet said about 350 visitors stopped by for a look, including former Mayor Patrick Burt, with whom he had a lengthy chat, he said.
Jacobson, the Stanford University professor who commissioned Bovet to build the first Bone Structure home in California, said as a professor of civil and environmental engineering, he has focused his academic career on finding large-scale renewable energy solutions to problems posed by air pollution and the climate crisis. That is why he turned to Bone Structure. The two-story four bedroom and three-bath home that Bone Structure designed for him on the Stanford campus is completely self-sufficient, Jacobson said.
"I have been able to sell electricity back to the grid, to Silicon Valley Clean Energy," said Jacobson, who also charges his electric vehicles at his residence. "I have not paid an electric, gasoline or natural gas bill in five years."
Jacobson said he had a positive experience working with Bone Structure on the design and planning of his home. From that initial contact through today, the Stanford professor said he remains impressed with the company's process and results.
"The construction process yields reduced waste compared to traditional construction," Jacobson said. "And then there are the big savings on energy."
Though it may only represent a small part of the Midpeninsula market at present, Palo Alto Realtor Brian Chancellor sees growth potential for this selective, high-end residential segment. "There is a well-informed, cutting-edge segment of the Midpeninsula luxury market very attuned to the issues of energy efficiency and sustainability," said Chancellor, who works in the Palo Alto office of Sereno Group.
"I think the Midpeninsula market is ripe for this type of home for the right type of homebuyers," he said. "There is absolutely a market for this here."
Get daily headlines sent straight to your inbox in our Express newsletter.
Get daily headlines sent straight to your inbox in our Express newsletter.
David Goll is a freelance writer.
Follow AlmanacNews.com and The Almanac on Twitter @almanacnews, Facebook and on Instagram @almanacnews for breaking news, local events, photos, videos and more.
Uploaded: Mon, Feb 6, 2023, 11:35 am It was the aspiration of Stanford's Atmosphere and Energy Program director to live in a net-zero home that was "strong, durable and could withstand a major earthquake, as well as termites and mold," that brought Canadian homebuilder Marc Bovet to Stanford in 2016 to build his first home in the state made of recycled steel. The prefab steel frame pieces arrived in one truckload from Canada and were snapped together in less than a week, creating the shell for Mark Jacobson's new 3,000-square-foot home, which reportedly cost an estimated $1.5 million. Solar panels coupled with Tesla Powerwall battery packs were installed to produce enough electricity to power the entire house plus two cars. ....................... Steely determination Since then, Bovet has exhibited steely determination to shake up the North American home market with steel frame, custom-built homes manufactured by his family-operated business, Bone Structure. Bovet now employs a staff of 40 architects, engineers, technologists and urban planners and operates a satellite office in San Francisco in addition to the company's Laval headquarters in Quebec, Canada. He has built hundreds of homes coast to coast in Canada and throughout California, including about two dozen along the Midpeninsula in Palo Alto, Menlo Park and Atherton. Bovet, who founded Bone Structure in 2005, said the company's steel construction system "just made sense." The goal, he said, is to create "homes that are not just energy efficient, but comfortable." ....................... Once on-site, steel pieces snap together like toy erector sets The company's homes are built from steel tubes manufactured in factories and designed to be attached together on-site. The framing system used in the homes is 88% recycled steel, mostly made of smashed cars. Each Bone Structure house is custom-designed and built with modular components, with no interior bearing walls. Bovet said homes range in size from 600 to 22,000 square feet. Bone Structure designs and plans homes for its owners, who then work with local builders and contractors to construct the homes, Bovet explained. Assembled in pre-built sections and then delivered to the construction site, Bovet likens the building process as similar to using such toys as erector sets or Legos. The horizontal steel pieces snap into place and are strong enough to support the interior finishes, including Sheetrock or tile, he said. Bovet said the pre-assembled sections have clear connections for specialists like plumbers and electricians to follow for their part in the construction. The pieces are "heavily engineered. All components are laser cut," said Bovet's son Charles, who received his master's degree in civil and environmental engineering and construction from Stanford University in 2013 and now serves as the company's vice president of business development. He noted that they use a patented "ankle" that allows some wiggle room in fitting those precisely cut components into the poured-concrete foundation. While the homes lend themselves to modern designs with long beam spans, the company's homes can be finished in stucco, brick or wood siding. The insulation, a combination of polystyrene panels and spray foam, are applied to the outside steel frame of the home and then covered up with whatever material the architect calls for. The plumbing and electrical infrastructure can be "threaded" through the steel frames through pre-cut holes. Bovet said he didn't start out using steel when he first entered the homebuilding sector. When he founded Bone Structure, Bovet used conventional building materials in his first project, but an unsuccessful launch led him to seek inspiration from above — literally — to move forward with his fledgling business. "I was driving near the (Montreal) airport when a jet thundered overhead," Bovet said, recalling his trip down a highway past Trudeau International Airport. "It occurred to me as it successfully took flight that the plane was not made of wood, but steel." He seized upon that inspiration. ....................... Less waste, more strength After "a lot of trial and error," Bovet said his company settled on the use of steel-frame residential structures, which he says avoids such wood structure deterioration problems like termites and mold, is more seismically safe, fire and flood resistant, and sustainable. Since the "bones" of his homes contain 88% recycled steel, the construction process does not create mountains of waste typical of conventional building sites, he added. Superior levels of energy efficiency are achieved through airtight insulation by combining rigid and foam insulation materials that can reduce heating and cooling costs by up to 90% compared to traditional construction, according to company information. Another distinctive feature of Bone Structure homes are floor-to-ceiling windows that afford sweeping views and accentuate the soya-based polyurethane insulation "thermal envelope" that reduces energy use, Bovet said. He views the Bone Structure process as a simplified one that makes the home-building experience a less stressful one for homeowners. Over the past seven years, Bone Structure has seen demand for their homes increase along the Midpeninsula. The company recently revealed its newest local structure to the public on Wilson Street in Palo Alto this past November. During the three-day open house for the two-story home, Bovet said about 350 visitors stopped by for a look, including former Mayor Patrick Burt, with whom he had a lengthy chat, he said. Jacobson, the Stanford University professor who commissioned Bovet to build the first Bone Structure home in California, said as a professor of civil and environmental engineering, he has focused his academic career on finding large-scale renewable energy solutions to problems posed by air pollution and the climate crisis. That is why he turned to Bone Structure. The two-story four bedroom and three-bath home that Bone Structure designed for him on the Stanford campus is completely self-sufficient, Jacobson said. "I have been able to sell electricity back to the grid, to Silicon Valley Clean Energy," said Jacobson, who also charges his electric vehicles at his residence. "I have not paid an electric, gasoline or natural gas bill in five years." Jacobson said he had a positive experience working with Bone Structure on the design and planning of his home. From that initial contact through today, the Stanford professor said he remains impressed with the company's process and results. "The construction process yields reduced waste compared to traditional construction," Jacobson said. "And then there are the big savings on energy." Though it may only represent a small part of the Midpeninsula market at present, Palo Alto Realtor Brian Chancellor sees growth potential for this selective, high-end residential segment. "There is a well-informed, cutting-edge segment of the Midpeninsula luxury market very attuned to the issues of energy efficiency and sustainability," said Chancellor, who works in the Palo Alto office of Sereno Group. "I think the Midpeninsula market is ripe for this type of home for the right type of homebuyers," he said. "There is absolutely a market for this here."
It was the aspiration of Stanford's Atmosphere and Energy Program director
to live in a net-zero home that was "strong, durable and could withstand a major earthquake, as well as termites and mold," that brought Canadian homebuilder Marc Bovet to Stanford in 2016 to build his first home in the state made of recycled steel. The prefab steel frame pieces arrived in one truckload from
Canada and were snapped together in less than a week, creating the shell for Mark Jacobson's new 3,000-square-foot home, which reportedly cost an estimated $1.5 million.
Solar panels coupled with Tesla Powerwall battery packs were installed to produce enough electricity to power the entire house plus two cars.
Since then, Bovet has exhibited steely determination to shake up the North American home market with steel frame, custom-built homes manufactured by his family-operated business, Bone Structure. Bovet now employs a staff of 40 architects, engineers, technologists and urban planners and operates a satellite office in San Francisco in addition to the company's Laval headquarters in Quebec, Canada. He has built hundreds of homes coast to coast in Canada and throughout California, including about two dozen along the Midpeninsula in Palo Alto, Menlo Park and Atherton.
Bovet, who founded Bone Structure in 2005, said the company's steel construction system "just made sense." The goal, he said, is to create "homes that are not just energy efficient, but comfortable."
Once on-site, steel pieces snap together like toy erector sets
The company's homes are built from steel tubes manufactured in factories and designed to be attached together on-site.
The framing system used in the homes is 88% recycled steel, mostly made of smashed cars. Each Bone Structure house is custom-designed and built with modular components, with no interior bearing walls.
Bovet said homes range in size from 600 to 22,000 square feet. Bone Structure designs and plans homes for its owners, who then work with local builders and contractors to construct the homes, Bovet explained.
Assembled in pre-built sections and then delivered to the construction site, Bovet likens the building process as similar to using such toys as erector sets
or Legos. The horizontal steel pieces snap into place and are strong enough to support the interior finishes, including Sheetrock or tile, he said.
Bovet said the pre-assembled sections have clear connections for specialists like plumbers and electricians to follow for their part in the construction.
The pieces are "heavily engineered. All components are laser cut," said Bovet's son Charles, who received his master's degree in civil and environmental engineering and construction from Stanford University in 2013 and now serves as the company's vice president of business development.
He noted that they use a patented "ankle" that allows some wiggle room in fitting those precisely cut components into the poured-concrete foundation.
While the homes lend themselves to modern designs with long beam spans, the company's homes can be finished in stucco, brick or wood siding. The insulation, a combination of polystyrene panels and spray foam, are applied to the outside steel frame of the home and then covered up with whatever material the architect calls for.
The plumbing and electrical infrastructure can be "threaded" through the steel frames through pre-cut holes. Bovet said he didn't start out using steel when he first entered the homebuilding sector.
When he founded Bone Structure, Bovet used conventional building materials in his first project, but an unsuccessful launch led him to seek inspiration from above — literally — to move forward with his fledgling business.
"I was driving near the (Montreal) airport when a jet thundered overhead," Bovet said, recalling his trip down a highway past Trudeau International Airport. "It occurred to me as it successfully took flight that the plane was not made of wood, but steel."
He seized upon that inspiration.
After "a lot of trial and error," Bovet said his company settled on the use of steel-frame residential structures, which he says avoids such wood structure deterioration problems like termites and mold, is more seismically safe, fire and flood resistant, and sustainable. Since the "bones" of his homes contain 88% recycled steel, the construction process does not create mountains of waste typical of conventional building sites, he added.
Superior levels of energy efficiency are achieved through airtight insulation by combining rigid and foam insulation materials that can reduce heating and cooling costs by up to 90% compared to traditional construction, according to company information.
Another distinctive feature of Bone Structure homes are floor-to-ceiling windows that afford sweeping views and accentuate the soya-based polyurethane insulation "thermal envelope" that reduces energy use, Bovet said.
He views the Bone Structure process as a simplified one that makes the home-building experience a less stressful one for homeowners. Over the past seven years, Bone Structure has seen demand for their homes increase along the Midpeninsula. The company recently revealed its newest local structure to the public on Wilson Street in Palo Alto this past November. During the three-day open house for the two-story home, Bovet said about 350 visitors stopped by for a look, including former Mayor Patrick Burt, with whom he had a lengthy chat, he said.
Jacobson, the Stanford University professor who commissioned Bovet to build the first Bone Structure home in California, said as a professor of civil and environmental engineering, he has focused his academic career on finding large-scale renewable energy solutions to problems posed by air pollution and the climate crisis. That is why he turned to Bone Structure. The two-story four bedroom and three-bath home that Bone Structure designed for him on the Stanford campus is completely self-sufficient, Jacobson said.
"I have been able to sell electricity back to the grid, to Silicon Valley Clean Energy," said Jacobson, who also charges his electric vehicles at his residence. "I have not paid an electric, gasoline or natural gas bill in five years."
Jacobson said he had a positive experience working with Bone Structure on the design and planning of his home. From that initial contact through today, the Stanford professor said he remains impressed with the company's process and results.
"The construction process yields reduced waste compared to traditional construction," Jacobson said. "And then there are the big savings on energy."
Though it may only represent a small part of the Midpeninsula market at present, Palo Alto Realtor Brian Chancellor sees growth potential for this selective, high-end residential segment. "There is a well-informed, cutting-edge segment of the Midpeninsula luxury market very attuned to the issues of energy efficiency and sustainability," said Chancellor, who works in the Palo Alto office of Sereno Group.
"I think the Midpeninsula market is ripe for this type of home for the right type of homebuyers," he said. "There is absolutely a market for this here."
David Goll is a freelance writer.
Home News TownSquare Blogs A&E Community Calendar Home & Real Estate Obituaries
Send News Tips Become a Member Print Edition/Archives Express / Weekend Express Special Pubs Circulation & Delivery Promotions
About Us Contact Us Advertising Info Place a Legal Notice Terms of Use Privacy Policy Palo Alto Online Mountain View Voice TheSixFifty.com Redwood City Pulse
© 2023 Almanac Online All rights reserved. Embarcadero Media PR MediaRelease Spotlight Mobile site
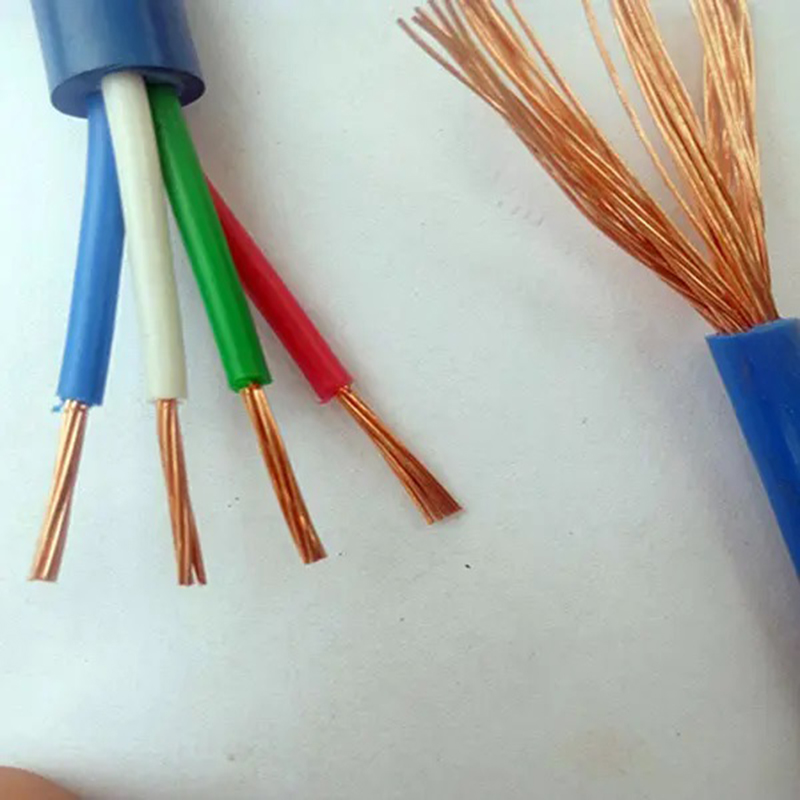
WDZN-BYJ fire-resistant Wire © 2023 Almanac Online. All rights reserved.